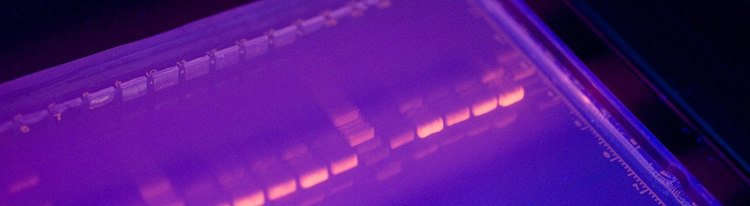
Aldevron Breakthrough Blog
Advanced HVAC - The Cornerstone of Aldevron Cleanrooms
July 21, 2020 / by Steve Chalfant
Aldevron has taken the basic design of heating, ventilation, and air conditioning systems (HVAC) for biological manufacturing clean rooms a step beyond the industry standard. The result is a super-clean system in our primary facility that allows us to produce the highest quality plasmid DNA, proteins and enzymes. In fact, from a cleanliness standpoint the Aldevron HVAC system is the cleanest I’ve worked on in my 20 years in the industry.
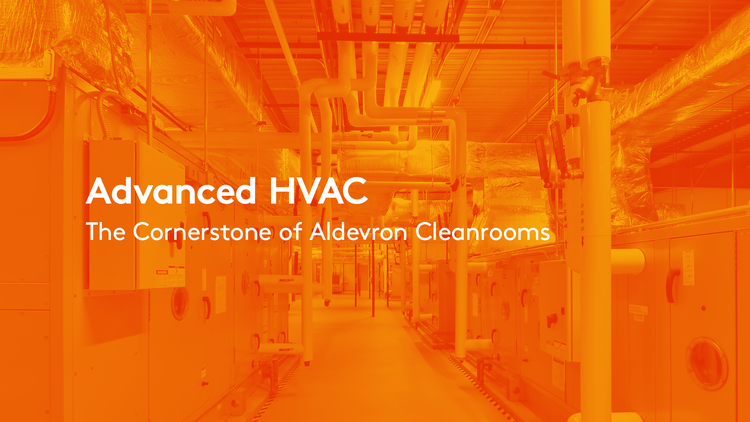
WHY HVAC IS IMPORTANT
Aldevron’s biological manufacturing clean rooms are required to meet US Food and Drug Administration (FDA) as well as European Union (EU) standards for Good Manufacturing Practice (GMP). To do that, we need to meet International Organization for Standardization (ISO) certifications for biological manufacturing, with various standards based on how many particulates are allowed to be in the air.
Given that, the HVAC system is the cornerstone of our manufacturing process. It manages temperature, humidity and pressurization, which allows us to completely control the environment, meet or exceed regulatory requirements and give our clients the confidence they need to select Aldevron as their partner.
THE ALDEVRON SYSTEM
The Aldevron HVAC system occupies 13,000 square feet, which is the majority of the second floor of our current facility.
It comprises a primary make-up air unit (MAU), nine air handling units (AHUs), and 258 high-efficiency particulate air (HEPA) filters. “Make-up air unit,” refers to its function, which is to continuously bring fresh air into the facility and replace air that has been exhausted.
The MAU is an advanced AHU that takes in 25,000 cubic meters of fresh air per minute. The air goes through 40-percent and 95-percent pre-filters, in addition to a set of heat exchangers that heat or cool the air, depending on the time of year and the temperature outside. From there, the system delivers the air to the nine additional AHUs to be filtered a second time. The AHUs then push the pre-filtered air into nine zones of GMP and GMP-Source® (GMP-S) manufacturing space, which includes 16,000 square feet in 49 separate clean rooms. Each of the rooms contains multiple ceiling mounted HEPA filters that remove 99.97 percent of particles as small as 0.3 microns.
THE ALDEVRON ADVANTAGES
The basic concepts of HVAC systems in biologics manufacturing are similar, with AHUs, HEPA filters, and filtration. Where the Aldevron system stands out is in its indoor location, pre-filtering and built-in redundancy.
First, indoor housing means our equipment is cleaner to begin with. While a lot of companies place AHUs on their roofs, ours are inside in a very clean area. Keeping the units indoors eliminates exposure to the elements, so they don’t rust or otherwise wear like equipment kept outside. Overall, it holds down maintenance costs and extends the equipment lifecycle.
Additionally, in terms of equipment, the MAU offers huge advantages from operational and cleanliness standpoints as well.
Most HVAC systems use rapid air handlers to bring fresh air in, filter it, and deliver it directly to the clean rooms. Not only do the AHUs tend to get dirty, but they also work harder. That, again, means more maintenance and associated costs.
By comparison, our MAU does all the heavy lifting of pulling in fresh air up front and pre-filtering it before it ever reaches the other AHUs. The results are that the AHUs do less work, perform more consistently, and require less maintenance. They also stay much cleaner over time. AHU filter change-outs generally need to be done every three months. Here, due to our innovative system, we only need to change them every six months, and they’re still clean.
Finally, redundancy is key for Aldevron and, more importantly, our clients.
In many facilities, when an AHU goes down manufacturing comes to a stop. Our MAU, meanwhile, contains a fan wall with multiple fans and motors. If one of them fails or needs service, we shut down that particular motor and ramp up another to continue pre-filtered fresh air delivery to each of the nine AHUs.
This adds another level of confidence for clients who rely on us to deliver high-quality products on time to ultimately serve the needs of patients.
CAMPUS & CAPACITY EXPANSION
As Aldevron grows, we’re incorporating another HVAC system like this one into our new buildings currently under construction on our Fargo, N.D. campus. The first, slated for completion by the first quarter of 2021, will increase our output capacity by 10 times over what it is today.
We learned a few things with our current facility related to efficient use of space and designed the new buildings accordingly. Other than that, the new HVAC system will be the same as what we have now.
It’s all part of our continuous investment in innovation that gives our clients advantages and helps reach our collective goal of bringing novel medicines to serve patients worldwide.